Steel production plays an important role in various industries, ranging from construction to manufacturing. As a versatile and durable material, steel is in high demand worldwide. the process of steel production is not without its challenges. here you know about the intricacies of steel production and explore the key obstacles faced by the industry. By understanding these challenges, we can identify effective strategies and solutions to overcome them, ensuring a seamless production process. So, let’s embark on a journey to overcome the challenges in steel production and strive for excellence!
What are the Challenges in Steel Production?
Steel production is a complex and demanding process that requires meticulous attention to detail. To ensure the highest quality output, manufacturers must navigate various challenges. Explore the most significant hurdles faced by the Steel industry and discover how they can be overcome.
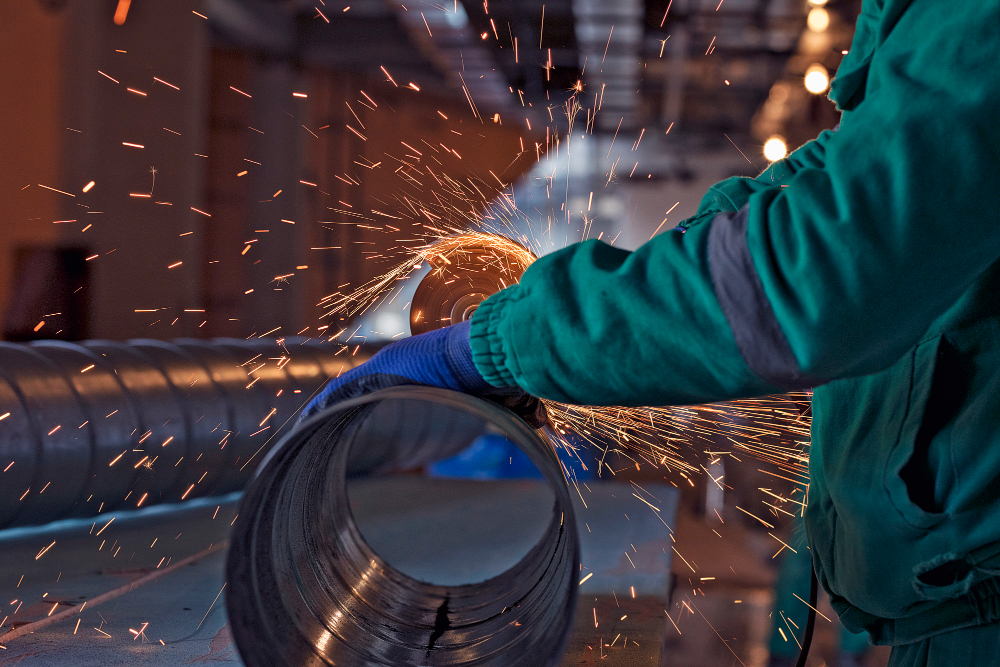
1. Raw Material Procurement: Ensuring a Steady Supply
The first challenge in steel production lies in the procurement of raw materials. Steel is primarily made from iron ore, coal, and limestone, which are not always readily available in sufficient quantities. Unstable market conditions, geopolitical factors, and transportation issues can disrupt the supply chain, leading to delays and increased costs. To overcome this challenge, steel producers need to establish robust relationships with suppliers, diversify their sourcing strategies, and invest in long-term agreements to secure a steady supply of raw materials.
2. Energy Management: Balancing Efficiency and Sustainability
Steel production is an energy-intensive process, requiring substantial amounts of electricity and fuel. Balancing the need for efficiency with sustainable practices is a significant challenge. Traditional steelmaking methods, such as the blast furnace route, are associated with high carbon emissions. technological advancements have paved the way for greener alternatives, such as electric arc furnaces and hydrogen-based processes. By investing in energy-efficient technologies and adopting renewable energy sources, steel producers can reduce their carbon footprint while maintaining productivity.
3. Environmental Regulations: Meeting Stringent Standards
With growing concerns about environmental sustainability, steel producers face increasing pressure to comply with stringent regulations. These regulations aim to reduce pollution, minimize waste generation, and promote eco-friendly practices. Adapting to these regulations can be a challenge, requiring substantial investments in pollution control technologies and waste management systems. Steel manufacturers must proactively embrace sustainable practices, implement efficient emission control measures, and invest in research and development for cleaner production techniques.
4. Cost Management: Balancing Profitability and Affordability
Cost management is a perpetual challenge in steel production. Fluctuating raw material prices, energy costs, and labor expenses can significantly impact the overall profitability of steel manufacturing. To overcome this challenge, steel producers need to optimize their operational efficiency, streamline their supply chain, and invest in automation and digitization. By leveraging advanced technologies, such as artificial intelligence and machine learning, steel manufacturers can enhance productivity, reduce costs, and remain competitive in the global market.
5. Quality Control: Ensuring Consistency and Reliability
Maintaining consistent quality standards is paramount in steel production. The properties of steel, such as strength, durability, and corrosion resistance, are critical for its intended applications. achieving consistent quality can be challenging due to variations in raw materials, process parameters, and equipment performance. Implementing stringent quality control measures, conducting regular inspections, and investing in advanced testing equipment can help overcome this challenge. collaboration with customers and feedback loops can enable continuous improvement and ensure customer satisfaction.
6. Skilled Workforce: Nurturing Talent and Expertise
The steel industry relies heavily on skilled workers who possess specialized knowledge and expertise. attracting and retaining a skilled workforce is an ongoing challenge. As older generations retire, there is a growing need to nurture the talent of younger workers and equip them with the necessary skills. Steel producers can overcome this challenge by establishing comprehensive training programs, collaborating with educational institutions, and providing opportunities for career advancement. By investing in the development of their workforce, steel manufacturers can ensure a continuous supply of skilled professionals and foster a culture of excellence.
7. Maintenance and Equipment Reliability: Minimizing Downtime
Ensuring the reliability of equipment and minimizing downtime is crucial in steel production. Unexpected breakdowns and maintenance requirements can disrupt the production schedule, leading to delays and increased costs. Implementing a robust maintenance strategy, including preventive maintenance and condition monitoring, can help identify potential issues before they escalate. leveraging data analytics and predictive maintenance technologies can optimize equipment performance, reduce unplanned downtime, and enhance overall operational efficiency.
8. Supply Chain Management: Streamlining Operations
Efficient supply chain management is essential to overcome the challenges in steel production. Coordinating the flow of raw materials, intermediate products, and finished goods requires careful planning and effective communication. Delays in the supply chain can result in inventory shortages, production bottlenecks, and customer dissatisfaction. Steel producers can overcome this challenge by adopting advanced supply chain management practices, such as just-in-time inventory systems, real-time tracking technologies, and collaborative partnerships with suppliers. Streamlining operations and ensuring seamless coordination can lead to cost savings, improved productivity, and enhanced customer service.
9. Market Volatility: Adapting to Changing Demand
The steel industry is susceptible to market volatility, with fluctuations in demand influenced by economic cycles, global trade dynamics, and geopolitical factors. Adapting to changing market conditions is essential for sustained success. Steel producers must closely monitor market trends, diversify their customer base, and explore new market segments. fostering innovation and product development can open doors to niche markets and differentiate them from competitors. By remaining agile and responsive to market changes, steel manufacturers can navigate uncertainties and maintain a competitive edge.
10. Technology Integration: Embracing Industry 4.0
The advent of Industry 4.0 technologies presents both opportunities and challenges for the steel industry. Embracing digitalization, automation, and connectivity can enhance productivity, improve process efficiency, and enable data-driven decision-making. integrating new technologies and transforming existing processes can be a complex undertaking. Steel producers must invest in research and development, pilot projects, and training initiatives to successfully implement Industry 4.0 solutions. By harnessing the power of advanced analytics, the Internet of Things (IoT), and artificial intelligence, the steel industry can overcome traditional limitations and achieve new levels of productivity and competitiveness.
Frequently Asked Questions (FAQs)
1. How can steel producers ensure a steady supply of raw materials?
To ensure a steady supply of raw materials, steel producers can establish robust relationships with suppliers, diversify sourcing strategies, and invest in long-term agreements. By maintaining open lines of communication and actively monitoring market conditions, manufacturers can mitigate the risks associated with raw material procurement.
2. What steps can steel manufacturers take to reduce their carbon footprint?
Steel manufacturers can reduce their carbon footprint by investing in energy-efficient technologies, adopting renewable energy sources, and exploring greener production methods such as electric arc furnaces and hydrogen-based processes. By prioritizing sustainability and embracing eco-friendly practices, the industry can contribute to environmental preservation.
3. How can steel producers navigate stringent environmental regulations?
To navigate stringent environmental regulations, steel producers can invest in pollution control technologies, implement efficient emission control measures, and establish comprehensive waste management systems. By complying with regulations and proactively adopting sustainable practices, manufacturers can ensure environmental responsibility and meet the standards set by regulatory authorities.
4. What strategies can steel manufacturers employ to optimize cost management?
Steel manufacturers can optimize cost management by streamlining their supply chain, investing in automation and digitization, and leveraging advanced technologies such as artificial intelligence and machine learning. By improving operational efficiency and reducing overhead costs, manufacturers can enhance profitability and remain competitive in the market.
5. How can steel producers maintain consistent quality standards?
To maintain consistent quality standards, steel producers can implement stringent quality control measures, conduct regular inspections, and invest in advanced testing equipment. Collaboration with customers and feedback loops can also facilitate continuous improvement and ensure that the end product meets the desired specifications.
6. How can the steel industry attract and retain a skilled workforce?
To attract and retain a skilled workforce, the steel industry can establish comprehensive training programs, collaborate with educational institutions, provide opportunities for career advancement, and create a conducive work environment. By investing in the development and growth of their employees, steel manufacturers can nurture talent and expertise within the industry.
Conclusion
Overcoming challenges in steel production is crucial to ensure a seamless and efficient manufacturing process. By addressing issues related to raw material procurement, energy management, environmental regulations, cost management, quality control, skilled workforce, maintenance, supply chain management, market volatility, and technology integration, the steel industry can strive for excellence.